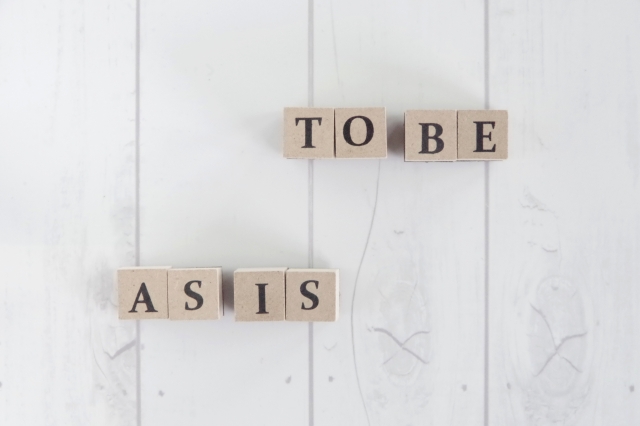
企業が目指す成長の道のりにおいて、羅針盤となるべき重要な分析手法があります。それが「ASIS TOBE分析」です。現状(AS-IS)を深く理解し、目指すべき理想の状態(TO-BE)を明確に描き出すことで、両者のギャップを可視化し、具体的な改善策へと繋げる強力なフレームワークとなります。
本稿では、ASIS TOBE分析の基本概念から実践的な進め方、そのビジネスメリット、そして具体的な成功事例までを紐解き、貴社の持続的な成長戦略を策定するための一助となる情報を提供します。
ASIS TOBE分析とは?現状と理想を結ぶ変革のフレームワーク
ASIS TOBE分析は、組織が現状の姿(AS-IS)を詳細に分析し、将来のあるべき理想の姿(TO-BE)を明確に定義することで、両者の間に存在する「ギャップ」を特定する手法です。このギャップこそが、取り組むべき課題であり、具体的な改善アクションを導き出す原動力となります。業務効率化、生産性向上、デジタル変革(DX)の推進など、企業のあらゆる変革活動において、その有効性が広く認識されています。
図解イメージ:
+-----------------+ +----------------+ +-----------------+
| 現状分析 | ---> | ギャップ分析 | ---> | 理想の状態 |
| (AS-IS) | | (現状と理想の差異)| | (TO-BE) |
+-----------------+ +-----------------+ +-----------------+
| | |
+-------------------------+-------------------------+
具体的な改善策の策定と実行
AS-IS(アズ・イズ):現状の徹底的な可視化
AS-IS分析では、企業の現状を多角的に捉えます。業務プロセス、組織構造、使用中のITシステム、従業員のスキル、顧客との関係性、情報の流れなど、ビジネスを構成するあらゆる要素を詳細に調査します。
- 定性的な調査: 従業員へのインタビュー、アンケート、ワークショップなどを通じて、日々の業務における課題、不満点、改善提案などを収集します。現場の生の声は、潜在的な問題点を浮き彫りにする上で不可欠です。
- 定量的な調査: 売上データ、コストデータ、業務時間データ、顧客満足度データなど、客観的な数値を収集・分析し、現状のパフォーマンスを評価します。KPI(重要業績評価指標)を設定し、現状の達成度合いを把握することも重要です。
- 業務プロセスの可視化: 業務の流れを図式化(業務フロー図など)することで、非効率な箇所やボトルネックとなっている部分を特定します。
TO-BE(トゥー・ビー):目指すべき未来像の明確化
TO-BE分析では、将来的にどのような状態を目指すのか、具体的な目標を設定します。これは単なる願望ではなく、市場の動向、競合の状況、自社の強み・弱みを総合的に考慮した上で、戦略的に定義される必要があります。
- 数値目標の設定: 売上成長率、市場シェア、顧客獲得数、コスト削減率、生産性向上率など、具体的なKPIを設定します。
- プロセス改善の設計: 新しい業務プロセス、効率的なワークフロー、自動化の導入などを検討します。
- システム導入・刷新の計画: 新しいITシステムやツールの導入、既存システムのアップグレードなどを検討します。
- 組織構造の再編: より効率的な組織体制、部門間の連携強化などを検討します。
ASIS TOBE分析の実践ステップ
ASIS TOBE分析は、以下の5つの段階を経て進行します。
ステップ1:ASIS(現状)分析 - 足元をしっかりと見つめる
現状分析では、上記の通り、定性的・定量的な両面から徹底的に情報を収集し、現状のビジネスの実態を詳細に把握します。この段階での丁寧な分析が、その後の改善活動の成否を左右します。
ステップ2:TOBE(理想)設計 - あるべき姿を鮮明に描く
次に、将来的にどのような状態を目指すのか、具体的な目標値を設定し、理想のビジネスモデルや業務プロセスを設計します。この際、関係部署との綿密な連携が不可欠であり、共通認識を持つことが重要です。
ステップ3:ギャップ分析 - 現状と理想の差異を特定する
ASIS分析で明らかになった現状と、TOBE設計で描いた理想の状態を比較し、その間に存在するギャップを明確にします。このギャップが、具体的な改善策を検討する上での重要な指標となります。
図解イメージ:
現状 (AS-IS)
+-----------+
| 業務A |
+-----+-----+
|
+-----+-----+ +-----------+
| 業務B | ---> | 理想の業務B' |
+-----+-----+ +-----------+
|
+-----+-----+
| 業務C |
+-----------+
<---- ギャップ ---->
ステップ4:改善策の策定と実行 - ギャップを埋めるアクションプラン
ギャップ分析の結果に基づき、現状を理想の状態に近づけるための具体的なアクションプランを策定し、実行に移します。これには、業務プロセスの再設計、ITシステムの導入、組織体制の変更、従業員のトレーニングなどが含まれます。
ステップ5:モニタリングと評価 - 効果測定と継続的改善
改善策の実行後は、設定したKPIを定期的にモニタリングし、効果を測定します。計画通りに進捗しているか、期待した成果が得られているかを評価し、必要に応じて改善策を見直し、PDCAサイクルを回すことで、持続的な改善を目指します。
ASIS TOBE分析のビジネスメリット
ASIS TOBE分析を導入することで、企業は以下のような多岐にわたるメリットを享受できます。
- 課題の明確化と優先順位付け: 潜在的な問題点や改善すべき点が明確になり、取り組むべき課題の優先順位をつけることができます。
- 効率的なリソース配分: 改善に必要なリソースを適切に割り振ることができ、無駄な投資を抑制し、効率的な資源活用が可能になります。
- 戦略的な意思決定の支援: データに基づいた現状分析と明確な将来目標設定により、戦略的な意思決定を支援します。
- 組織全体の共通認識の醸成: 分析プロセスに関わることで、従業員全体の課題認識が高まり、目標達成に向けた一体感が生まれます。
- 変革プロジェクトの成功率向上: 計画的かつ段階的な改善アプローチにより、変革プロジェクトの失敗リスクを低減し、成功へと導きます。
成功事例:製造業における生産ラインの最適化
ある中堅製造業では、長年の経験に基づいた職人の技術に依存した生産ラインがボトルネックとなり、生産性の向上と品質の安定化が課題となっていました。
ASIS分析: 生産工程における各作業時間、不良発生率、設備の稼働状況などを詳細に分析した結果、手作業による組み立て工程に時間がかかり、人的ミスによる不良が多いことが判明しました。また、熟練作業者と新人作業者のスキル差が大きく、品質のばらつきも課題でした。
TOBE設計: 生産ラインの自動化を推進し、ロボットによる組み立て工程を導入することで、生産性の向上と品質の安定化を目指しました。また、新人作業者でも一定の品質を確保できるよう、作業手順の標準化とマニュアル化を徹底しました。
ギャップ分析: 現状の手作業中心の生産ラインと、自動化された理想の生産ラインとの間には、生産性、品質、コスト、作業時間など、多くのギャップが存在することが明らかになりました。
改善策の実行: 最新の産業用ロボットを導入し、組み立て工程を自動化しました。また、作業手順を詳細にマニュアル化し、新人研修プログラムを充実させました。さらに、生産管理システムを導入し、リアルタイムでの進捗状況の把握と品質管理を徹底しました。
モニタリングと評価: 自動化ラインの稼働状況、不良発生率、生産時間などをKPIとして設定し、定期的にモニタリングしました。その結果、生産性は25%向上し、不良発生率は15%削減、作業時間も大幅に短縮されました。
まとめ:ASIS TOBE分析で未来を拓く
ASIS TOBE分析は、企業が現状の課題を乗り越え、理想の未来を実現するための強力な羅針盤となります。
現状を客観的に把握し、目指すべき姿を明確に描くことで、具体的な改善策が見えてきます。
変化の激しい現代において、ASIS TOBE分析は、持続的な成長と競争力強化を実現するための不可欠なツールと言えるでしょう。
貴社もぜひ、ASIS TOBE分析を導入し、変革への一歩を踏み出してみてはいかがでしょうか。